Why do you keep spending money on low-intensity concrete?
To prevent problems, we want you to know before offering a concrete construction.
Concrete construction is a one-shot deal!!
After construction of concrete, you have to use it for several tens of years. It is unrealistic to replace it so many times. Therefore, it is very important to decide how the construction will go with which concrete.
From "strength" to "density"
The construction method we recommend here was created by a developer who had doubt why the conventional methods only had focused on "strength" of concrete.
Durable concrete having more than 200 years of life time: Simultaneous one-time construction of high-density concrete by re-vibration
The method provides not only strength, but also high-density to prevent cracking. Reduction in the number of processes and man power realizes lower costs than the conventional methods!
They say in Japan, we have already used 10 billion square meters of concrete, and generally the life of the concrete structures is 50 to 50 years. As a matter of fact, some structures need rebuilding in 20 to 30 years.
Many customers surely worry about floors durability (life period). They are serious concerns for customers who repair and renew the old structures. Everyone has doubts about the durability, and hardly decide whether to renew the concrete floor of the existing frame in the repair construction.
What influence the durability and life period is a "crack." Cracks occur due to various reasons. Now, we often see advanced concrete, low-slump concrete or concrete containing water reducing agent, but unfortunately, some of them are cracked after only 1 or 2 years from the start of service.
As a result of learning from the existing concrete in the repair sites and from the viewpoint of construction operator, we consider the problem is intensive focus on strength, instead of density.
Look a concrete core, and you find even the concrete with strength has a lot of bubbles inside every core. This causes cracks of all kinds.
How high strength the concrete has, the concrete with bubbles suffers from cracks, and even promotes neutralization, and accordingly cannot provide life period that you need.
Theoretical figures are not important for concrete constructions. The actual processes are everything.
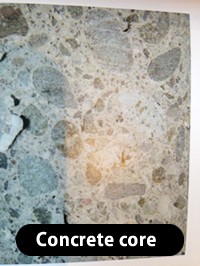
We create realistic durable concrete having more than 200 years of life time, with high density, instead of high strength.
Comparison between re-vibration construction method and conventional construction methods
Difference of re-vibrating roller and compactor surfer, and conventional construction methods
The re-vibrating construction method is essential for high-density concrete constructions, and has existed in the industry as an acclaimed method. However in fact, the existing re-vibrating construction method is very difficult to handle. The new construction method makes the previously prohibited re-vibrating construction method after leveling easier, from the aspect of quality and operability, and get a lot of attention. Now, major construction companies and every organization conduct many test constructions, and the private construction sites start moving to practical use of the re-vibrating construction method.
- The method with which an operator re-enters inside after leveling the concrete and applies vibration makes the floor level uneven, and remaining footprints may let air go inside. Also, concerning the floor level with this method, surface treatment accuracy is not so high.
In addition, when the operator levels the hard surface, the surface gets rough like a honeycomb, which makes removal of bubbles difficult, or too quick drying of the surface makes pressing by a trowel defective.
- Vibration tampers make the conventional tamping works easier, and at the same time, give even vibration to a whole area, compared to application of vibration. However, when the operator uses a tamper after leveling the concrete, the tamper board goes under the floor, and it is difficult to remove wave traces, unevenness, and footprints on the floor level. Although their vibrator functions are sufficient, they are not proper for re-vibrating operations.
Also, the conventional tampers have narrow and small boards. Therefore, their surface compaction area is not proper for re-vibrating operations.
This is the "re-vibrating construction method" in the spotlight!!
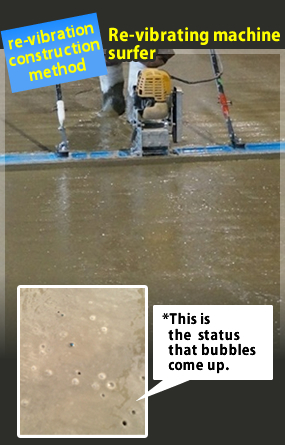
Using difference of vertical force and horizontal force applied on the surface concrete by vibration of the machine and the board makes buoyant force, and the board raises on the leveling concrete, and at the same time, gives strong frequency vibration. It is a big difference from the other tampers.
This method allows re-vibrating of the concrete while keeping the floor level, and since the board raises even on the dirt floor after leveling, it does not damage the floor level and makes leveling possible safely.
By keeping the surface compaction area suitable for re-vibrating high density, the method ensures sufficient surface compaction, and allows total and even leveling without remaining footprints, removal of bubbles, voids, and water passages, and precise formation of hardened structure inside the concrete. Evenly, closely, and securely, density improves.
High density concrete construction method
①Leveling surfer
First, we level the concrete carefully. We prepare two vibrators for one pump, and apply vibration precisely and closely. Leveling is the most important process for dirt concrete. Following the operation procedure, we level the concrete carefully and perfectly. These steps are ordinary.
Before the bleeding process starts little while after the leveling process completes, we re-vibrate the concrete with the re-vibrating machine (surfer).
Re-vibrating of the concrete which once has been leveled significantly increases the concrete density. Although the concrete has been vibrated carefully and precisely as mentioned above, many bubbles emerge by re-vibration. Unnecessary excessive water also emerges, water passages and voids which cause cracks are eliminated, and removed water emerges on the surface. Increase of the density logically eliminates bubbles and voids, and accordingly, the strength increases.
We compact the floor by re-vibration, check bubbles, and confirm that the density goes up. To eliminate voids and remove water passages completely is a specific crack prevention measure during the leveling process.
②Concrete roughening: Roughening machine
After vibrating the concrete, we use a roughening machine for the next process. We make lines individually around 10 mm wide and 5 mm deep on the compacted concrete.
③Resin spreading: Spreader
Then, with a spreader, we pour liquid containing resin evenly. We spread it in an area where the wall and the base board contact with a watering pot, and pat with a trowel presser.
We are trying to make a poured flooring finishing and a reinforcement simultaneously at one time. A strong monolithic floor can be created by such simultaneous and one-time construction, and generates no peeling or floating.
④Surface compaction: Lorry
This machine looks like a roughing machine above, but is called "lorry." After we confirm that the spread liquid penetrates, with this machine, we press the floor with a roller and also vibrates the concrete further. This process combines the concrete and the liquid, and at the same time, removes surface bubbles of the rough surface floor. To make the hardened structure of the surface close reduces cracks occurring on the surface drastically.
Cracks are generated by causes under the floor and causes on the surface. In case of cracks generated by the causes on the surface, the hardened structure of the surface is thin, and fine bubbles on the surface react with carbon dioxide, causing cracks and neutralization. To prevent this problem, the hardened structure of the surface is dense.
Since this lorry is originally very effective for adjusting unevenness of floors, it levels the floor effectively, in addition to densifying the surface. With this lorry, we cross vertically and horizontally, as removing unevenness, level the surface with a reversing trowel attached to the lorry, and then, leave the floor for a while.
⑤Circular pressing: Trowel
We leave the floor until the surface gets dry, and press it roundly with a trowel. Then, when the surface congeals, we cross a machine trowel horizontally and vertically, and level the floor as checking watering condition of the cement paste.
To perform circular pressing before putting the trowel, when we circulate firmly, the disk is hardly contact closely to the surface because the surface is hardened, and some parts are not pressed by the disk. However, with this method, we have already adjusted unevenness with the lorry in the previous process, so, we can perform circular pressing surprisingly smoothly even when we circulate firmly. This is because the surface accuracy is excellent, and therefore the trowel goes smoothly and evenly. Before this step, we quickly finish edge parts and other parts with variable drying conditions with a Fresno or trowel presser before insufficient pressing occurs.
⑥Finishing: Handman
The surface finishing tool is called Handman, a machine trowel equipped with a super trowel. When using Handman, we have to remove even small protrusions, concaves, and blisters because they affect the surface finishing appearance directly. We have to contact the whole area of the super trowel equipped with the Handman machine with the concrete surface completely.
Therefore, application of Handman needs smooth and thoroughly flat substrate prepared by unevenness adjustment and circular pressing. If we skip this process, the surface is deteriorated. Smooth surface floors are created by all these processes focusing on quality.
- We consider that this method is the next generation concrete finishing construction method, allowing simultaneous construction at one time, based on the high density concrete providing thorough crack prevention and the surface reinforcement, throughout the substrate concrete preparation process to the surface finishing process.
First of all, the biggest advantages of this method are short construction period and process and reduced total cost, thanks to the simultaneous construction at one time. The method allowing the simultaneous construction at one time solves all problems concerning preparation of project costs and manpower, and schedule adjustment, process problems about curing period and substrate clearing process, and other difficult schedule adjustment combined with the other types of construction works. We believe that high technology and reliable quality satisfy not only site managers but also end users, and accordingly contribute to improvement of customer satisfactions.